PRESSURE FORMING
Lormac Plastics has over 40 years of experience in pressure forming of quality custom parts.
Pressure Forming is a sophisticated version of the vacuum forming process utilizing air pressure as a forming aid to increase the detail on the mold side. The pressure applied (up to 100 pounds per square inch) is approximately five times higher than with vacuum forming, which makes it possible to obtain highly detailed features at close tolerances.
Pressure forming is proving to be a valuable technique for the computer, electronic, furniture, industrial, and medical industries. It is enabling them to get parts into the market quickly that have the look of injection molding, without the lead times or tooling expense. Pressure forming can provide the structural integrity, aesthetics and design flexibility usually found only in injection molded parts.
Benefits of pressure forming:
- sharp edges
- under cuts and reverse drafts
- tight corner radii
- multiple-textured surfaces
- better control of wall thickness for structural integrity
- embossed lettering and other fine surface detail
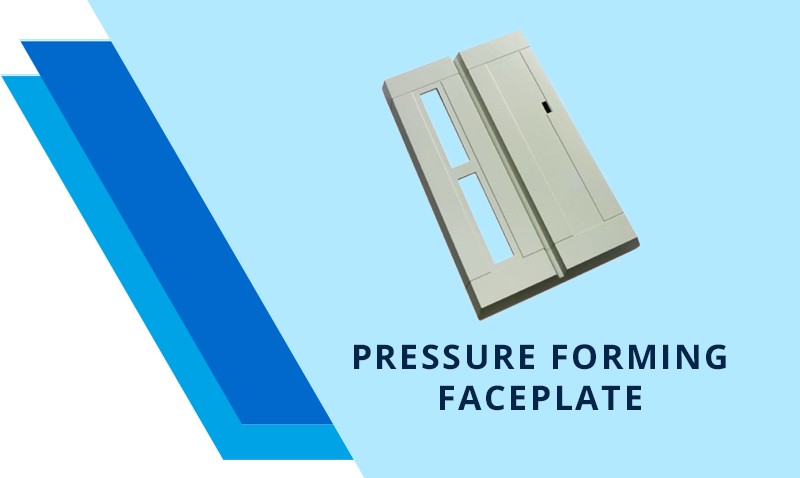
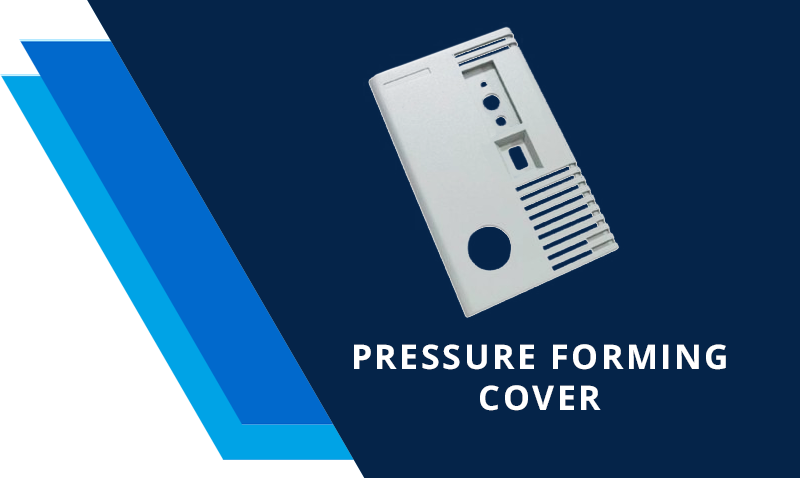
THE THERMO PRESSURE FORMING PROCESS
Clamping
The clamp frame ensures the plastic sheet is held firmly in place during the pressure forming process.
Heating
Radiant heaters are normally used to heat the sheet which has been positioned over the aperture of the pressure forming machine. For thicker sheet both surfaces may need to be heated and more sophisticated machines allow this. Heaters move into position both above and below the sheet.
Pressure Forming
The hot sheet is transferred to the forming station, the upper mold (or pressure box) and lower mold are brought together and compressed air is introduced through the pressure box pushing the material against the mold.
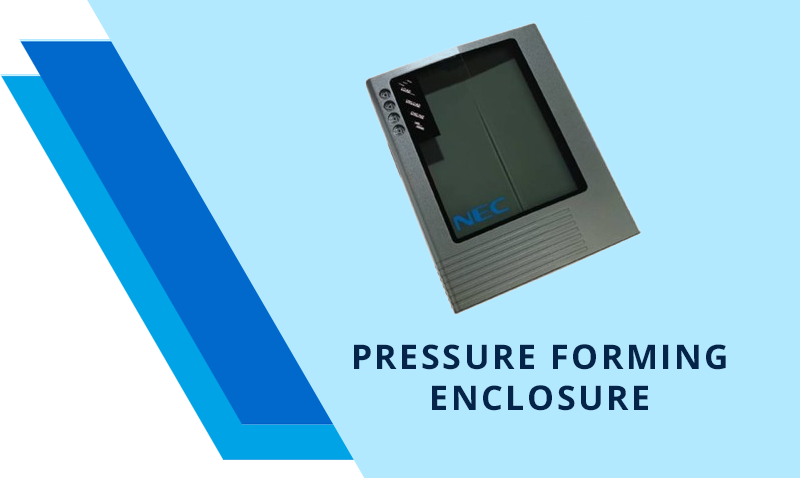
Plug Assist
Where a deep draw is required a top “plug” may be used to push material into the mold during the pressure forming process.
Cooling and Release
The material is allowed to cool. The cooling process may be shortened with blown air or even a fine water spray. The molding may then be released from the mold by introducing a small air pressure.
Finishing
After pressure forming the part, any mold finishing may be performed, such as: trimming, cutting, drilling, polishing, painting, screening, etc.
If you are in need of pressure forming for both prototype and production or if you have any questions regarding the pressure forming process, optimal part design for pressure forming, or any other related questions, please reach out to us at Lormac Plastics. With over 40 years in business and over 100 years of pressure forming experience, we are your trusted source.
Helpful Links
Links to other sites containing data around the vacuum forming process: