THERMOFORMING
Lormac Plastics has over 50 years of thermoforming experience, producing quality custom plastic parts in San Diego. Our experienced staff has a wealth of knowledge with a combined 150+ years of work at Lormac. If you can dream it, we can produce it.
Our fully automated, state of the art, computer controlled machines can form plastic sheet from .04” to .50” thick. Current Thermoforming equipment includes:
- 48×96” Single Station Thermoforming Machine
- 60×72” Single Station Thermoforming Machine
- 48×72” Rotary Thermoforming Machine
- 48×72” Double Ended Thermoforming Machine
- 48×48” Single Station Thermoforming Machine
- 36×36” Single Station Thermoforming Machine
Vacuum forming offers several processing advantages over other forming processes. Low vacuum forming pressures are used thus enabling comparatively low cost tooling.
Since the vacuum forming process uses low pressures, the molds can be made of cost effective materials and mold fabrication time can be reasonably short. The vacuum forming process is perfect for prototyping production parts and for small and medium sized production runs.
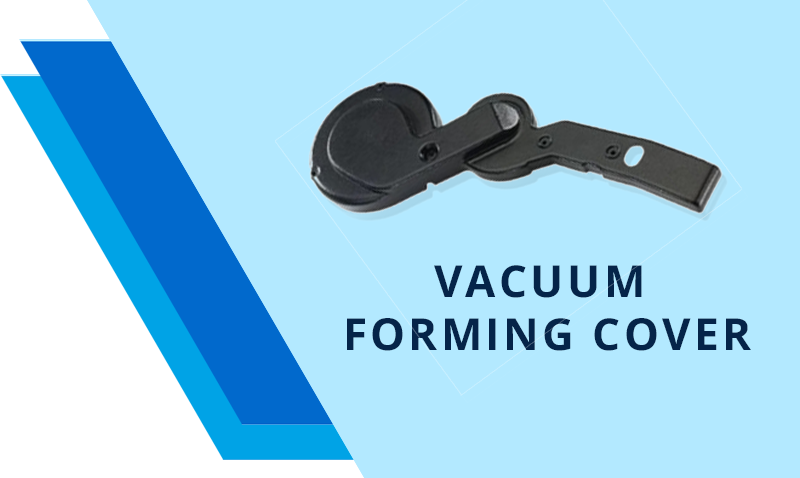
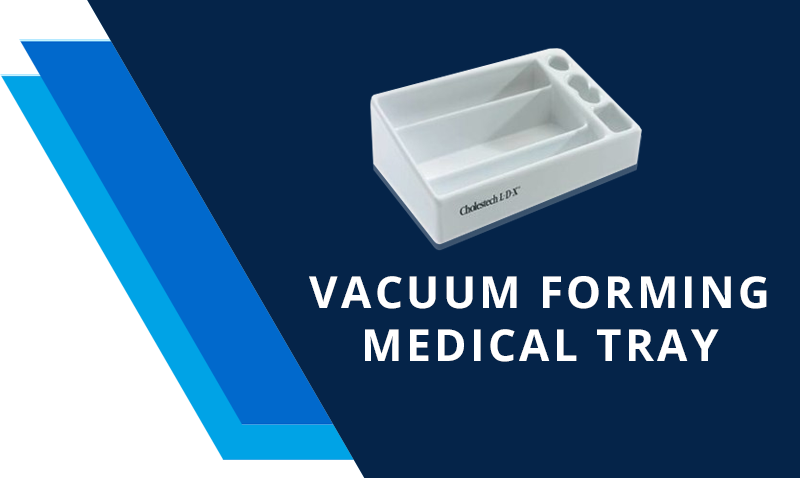
THE THERMAL VACUUM FORMING PROCESS
Clamping
The clamp frame ensures the plastic sheet is held firmly in place during the vacuum forming process.
Heating
Radiant heaters are used to heat the sheet which has been positioned over the aperture of the vacuum forming machine. Thicker sheets may require both surfaces be be heated by moving heaters into position both above and below the sheet.
Pre-stretch
Is used to achieve “even” wall thickness. Air is introduced to blow a small “bubble” and the mold is then raised into the pre-stretched sheet.
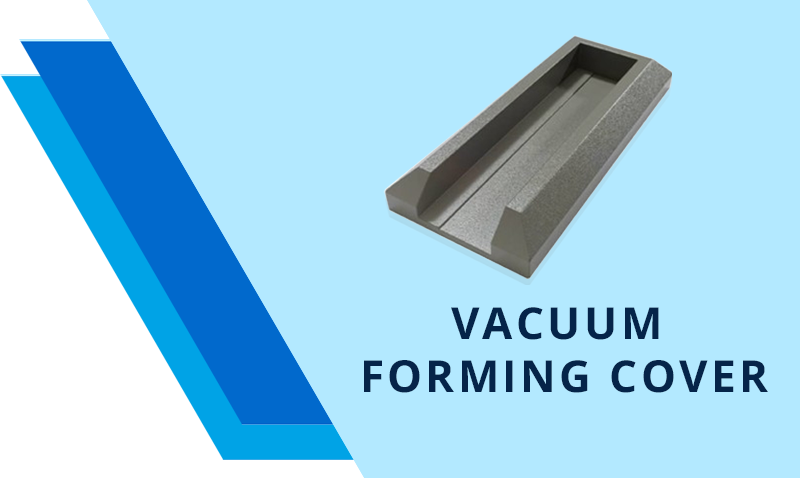
Vacuum Forming
A vacuum is applied, the sheet is drawn into tight contact with the mold and the mold detail is picked up.
Plug Assist
Where a deep draw is required, a top “plug” may be used to push material into the mold during the vacuum forming process retaining even wall thickness.
Cooling and Release
The material is allowed to cool. The cooling process may be shortened with blown air and the molding is then released from the mold by introducing air pressure.
Finishing
After the part is vacuum formed, secondary services are performed, including: trimming, cutting, drilling, assembling, polishing, painting, and screening.
If you are in need of vacuum forming for both prototype and production or if you have any questions regarding the vacuum forming process, optimal part design for vacuum forming, or any other related questions, please reach out to us at Lormac Plastics. With over 40 years in business and over 100 years of vacuum forming experience, we are your trusted source.
Helpful Links
Links to other sites containing data around the vacuum forming process: